
Support Bracket
A 5-man team led by myself were tasked with the following:
Design a bracket to support a load offset from a fixture
Manufactured by SLS process using Fine Polyamide PA2200
Maximum component size of 380x30x60mm before assembly
Given budget of £150
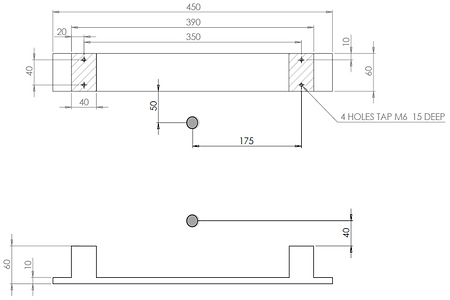

Team Objectives
Maximise load to cost ratio
Initial calculations would be done by hand
Design would be done using CAD SolidWorks
Finite Element Analysis using ANSYS for iteration development

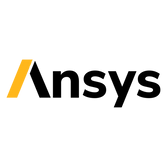
Theory
Strength to weight ratio calculations concluded I-beam design to be the most cost-effective

Concept
Further from initial calculations the first bracket is made in solid works with the chosen I-beam cross-section
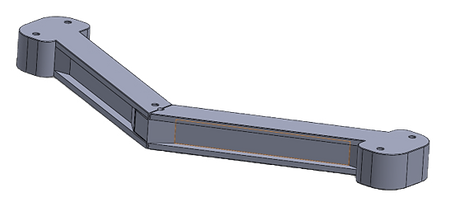
Simulation
Finite-Element-Analysis is then enacted with boundary conditions applied, simulating deformation under expected loads
Quality Check
With limited elements available, meshes are focused in detail along the most significant areas of stress concentration found.
These meshes are further examined and adjusted to accommodate the curved edges, joints, and fillets to produce an overall analysis with respectable element quality.
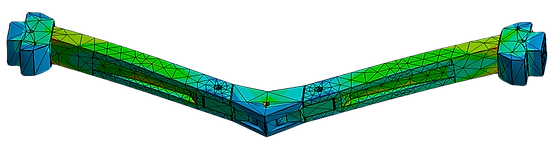

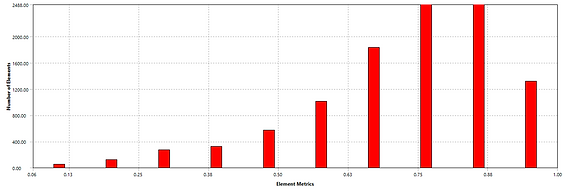
Refinement
The bracket is then refined and improved where causes of failure are found, and an iterative process of modelling to FEA is enacted to arrive at a final and optimised support bracket.




Final Product






With the successful material reduction and optimisation along each stage, the final product uses 60% of the available budget